During the commissioning process, communication is key at every step. It is important to use effective means of communication so that everyone involved remains fully aware of project updates at all times.
So, are you aware of the best practices a commissioning management company can integrate into the construction phase to make the entire process more efficient and effective? Here we discuss the commissioning best practices to follow during the crucial construction phase.
Holding a Terrific Initial Meeting
If conducted in a proper manner, the kickoff meeting should make the teams involved in the project feel confident that the commissioning management system in place will help ensure the success of the project. Discussed below are some of the best practices for the initial meeting:
- The meeting must be scheduled very thoughtfully and on time. Ideally, the meeting should not occur too early. This is because in such a case, contractors might forget about the commissioning process if enough time passes by. On the contrary, if the meeting happens when equipment installation has already started, you will potentially miss key opportunities to assess submittals and inform the process. The ideal time to hold a kickoff meeting is when contractors are present on the site and the construction phase has just commenced, but the equipment is yet to be installed.
- No matter how obvious it may seem to everyone, the initial meeting must include a complete assessment of the commissioning process. Providing the list of equipment that needs to be commissioned, including pre-functional checklists, and testing durations and prerequisites is important to make every team member understand the expectations completely. These days, an advanced commissioning management software product can be used, which simplifies the entire process considerably.
- To maintain the momentum of the meeting, consider taking a walk through the site just after the meeting as well as greeting and interacting with site contractors while showing to them that you are genuinely interested in their work and trying to have a better understanding of the project with focused observation.
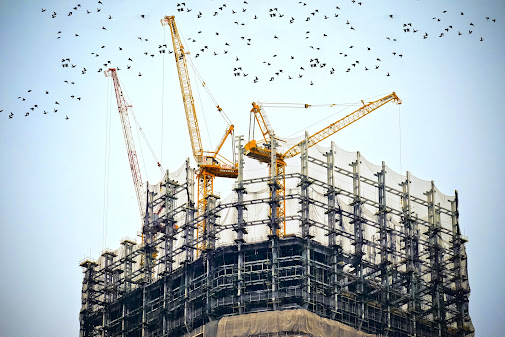
Completing Pre-Functional Checklists by the Commissioning Authority
Instead of depending on equipment installation contractors, the commissioning authority should take charge of completing pre-functional checklists. The commissioning authority is in a strong position to check the proper installation of equipment early on, prevent systemic issues from occurring, and act as a supporter of the owner in the most effective manner.
Be Part of the Solution
Project teams admire commissioning authorities who dare to think beyond just preparing lists of problems – and try to come up with the solution. The commissioning deficiencies log is a crucial tool for communication when it is about discovering deficiencies that can’t be resolved instantly. All deficiencies are assigned to the relevant team members. The commissioning deficiencies log should define all deficiencies clearly while offering recommendations to resolve them. While completing the pre-functional checklist on site, the commissioning authority should try to build rapport with the project team that is responsible for the installation of equipment. So, when deficiencies are identified, this will help the commissioning authority in understanding whom they should approach, to discuss the deficiencies so as to either get recommendations for faster resolutions or resolve them on the spot.
Customise Functional Performance Testing (FPT)
FPT documentation should be completed once submittals are approved. Besides reflecting specific manufacturer operational and installation requirements, it should include test procedures developed over many years of commissioning-specific experience. Use control sequences that are produced by the design engineer to check the response of equipment to changes in the status, such as enabling an economizer mode or transitioning from cooling to heating. Does the equipment set back once set points are attained? Does equipment for power backup begin to function during a sudden power failure? Is the interface for direct digital controls complete, without errors? These questions and more are satisfactorily answered when the commissioning authority has exhaustive FPT documentation, administers test procedures in an organised manner, and records the results clearly and accurately, so that testing can be done repeatedly in the future during the time of recommissioning.
Final Words
The best value of commissioning is achieved during the design phase when low costs and high impact are most beneficial. As the project transitions into the construction phase, cost avoidance becomes more challenging. The best practices discussed above will help ensure the project teams are fully informed, pricey equipment failures are prevented and the project is prepared for a successful testing and acceptance phase.
Comments
Post a Comment